27 août 2008
3
27
/08
/août
/2008
00:00
Nach dem Bau eines Freestyle-Kayaks, und weil mir die Form gefällt, habe ich dieses Jahr entschieden eine Nefativform davon zu machen, um ein Kayak unter Vacuum bauen zu können.
Ich habe zuerst das Positivmodell vom vergangenen Jahr so schön vorbereitet wie mir meine Nerven es ermöglicht haben. Es braucht mehr Zeit als man zuerst denkt, wenn man eine perfekte Oberfläche bekommen will. Nachdem ich alle Unebenheiten geschliefen hatte, habe ich das Modell zwei Mal mit Polyesterharz lakiert, und dann mit Wasserfestem Schleifpapier (Korngrößen 120, 360 und schließlich 600) weiter geschliefen. Nach Polierung und Trennmittelauftrag (Trennwachs + Trennlack) ist das Modell fertig um den Negativabdruck zu bauen:
Mein Negativmodell ist nicht wie ein normales Negativmodell gebaut, sondern ich habe eine ähnliche Laminierung gemacht wie für ein Kajak, damit ich es auch als Boot benützen kann anstatt es zu wegschmeissen nachdem ich ein Paar Boote damit gebaut habe.
Oberes Teil gleich nach Laminierung:
Unteres Teil nach Trennung:
Um die Dünnheit der Laminierung und die darausfolgende Biegsamkeit zu kompensieren, habe ich Verstärkungen gebaut. Dies war nicht sehr klug: das Modell hat sich genau um die Verstärkungen verformt (weil die Laminierung zu dünn war):
Die Vakuumpumpe:
Es ist oft umstritten ob sich Hobbybastler eine billige - dennoch effektive - Vakuumpumpe aus Eiskastenkompressoren bauen können. Oft wird argumentiert, dass so eine Pumpe nicht "stark" genug ist, usw... Solche Aussagen mögen etwas Richtiges an sich haben. Es gibt aber zwei Parametern, welche man beobachten muss um diese Frage zu beantworten: das Vakum, und den Durchfluss die die Pumpe leistet:
- das Vakuum ist kein Problem, weil ein gut funktionnierender Eiskastenkompressor ohne Problem einen restlichen Druck von 100 mBar (oder -900 mBar bezogen auf die 1000 mBar des atmosphärischen Drucks) erzielen kann, also 900 g/cm². Das ist mehr als genug um eine Laminierung zusammen zu pressen.
- der Durchfluss ist das limitierende Parameter: Er ist klein, und der Vakuumsack in dem das laminierte Stück gegeben wird, muss dicht sein. Auch kleine Löcher haben den Effekt, dass die Pumpe nicht nachkommen kann, und das gewünschte Vakuum (für mich mit meiner Arbeitsmethode, etwa 500 mBar) nicht erreichen kann.
Mit diesen Ideen im Kopf habe ich ein System mit zwei Eiskastenpumpen gebaut, damit der Durchfluss größer ist:
Es gibt ein Regulationssystem das ich nicht selber gebaut habe, sondern mein Großvater der ein solches System seit Jahren zwecks Modellbau benützt. Die Idee ist Einfach: der Vacuum zieht eine Membrane von einer Seite, und eine Ziehfeder zieht von der anderen Seite. Man muss das System mit einem Vakuometer eichen, und es gibt ein elektrisches System was den Strom abschaltet wenn das Vakuum stärker ist als die Ziehfeder... so viel dazu.
Und jetzt der spannende Teil: Kajakbau unter Vakuum!!!
Nach einigen Proben habe ich gefunden, dass ein Vakuum von 500 mbar (= 1/2 atmosphäre, oder 500 mg/cm²) den Besten Kompromis zwischen Pressung des Laminats und Evakuierung das Harzes bietet. Es werden ca. 20% des Harzes evakuiert.
Zuerst legt man eine Schicht Gelcoat. In meinem Fall es ist Epoxyharz, wozu ich Aerosil gemischt habe: ein Pulver welches zur Verdickung des Harzes dient. Das Gelcoat ist orange, und ich habe es an einigen Stellen durchsichtig gelassen (man sieht das gelbe Modell):
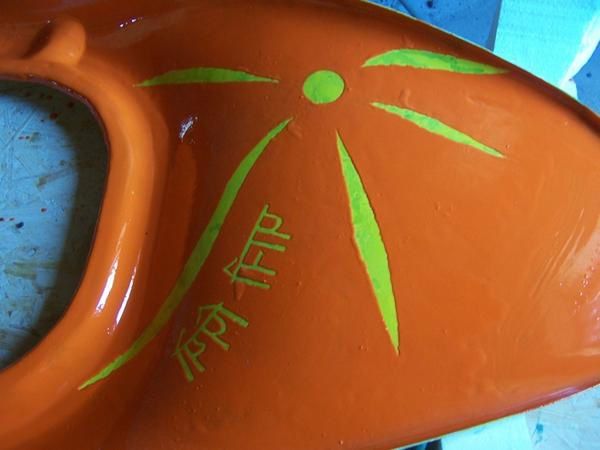
Nach der Laminierung legt man zwei Materialien, die für den Vacuumbau notwendig sind (Bild):
- eine perforierte Plastikfolie, die das überflüssige Harz durchlässt
- einen Filz, der das Harz aufsaugt (Drainage).

Dann wird das Ganze in einen Sack gegeben, dicht geschlossen, und die Pumpe wird für ca. 8h. eingeschalten.
Am nächsten Tag kann man das Laminat auspacken. Man sieht auf folgendem Bild den Filz, der das Harz gesaugt hat (schwarze Punkte). Das Relief ist das Sandwich welches ich mit Extrudierschaum gemacht habe. Dieser Schaum wird in das Laminat integriert und macht es steifer:
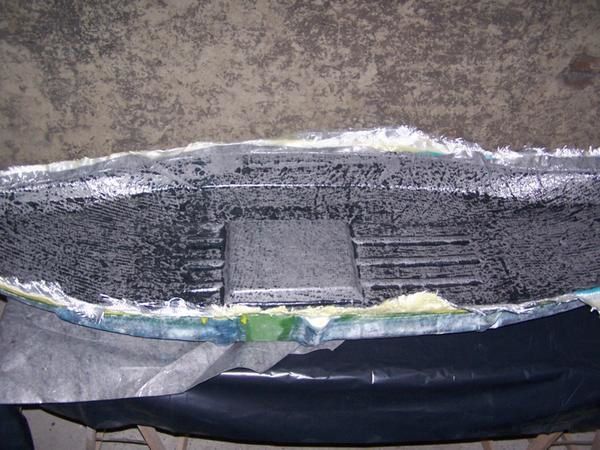
Das nächste Bild zeigt die Trennfolie nach Entfernung des Filzes:
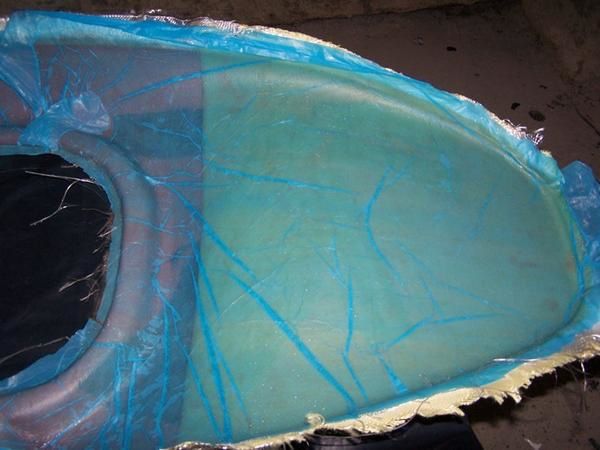
Man muss dann nur mehr die zwei Teilen zusammenkleben, einen Sitz bauen, und das Boot ist fertig!



7 juillet 2008
1
07
/07
/juillet
/2008
15:45
Dimanche 6 Juillet: La coque.
Detail de la stratification: le kevlar est epais (400 g) donc je me suis limite a 5 couches completes (KVVVV) + renfort Kevlar sur tout le fond plat et aux pointes + extra renforts Kevlar sur les cares. A cela s'ajoutent 2 couches de verre (rowing 280 g) sur le fond plat par dessus les bandes de sandwich. Au final, le fond plat a bien 8 couches, ce qui devrait suffire a rigidifier en plus du sandwich et de la plaque de styro pour la surelevation de siege.
Attention tout de meme avec le styro, il semble qu'il continue a degazer sur toute sa duree de vie ce qui augmente les risques de delaminage et n'en ferait pas le materiau ideal pour la mise en sandwich. Voir sur ce lien pour plus de details: http://www.eauxvives.org/forum/topic.asp?TOPIC_ID=16515 UPDATE: apres 4 ans depuis la construction du bateau, je n'ai remarque aucun probleme.
J'ai mis sous vide leger (env. 500 mbar) compte tenu des test faits lors de la construction de sieges. J'avais eu le probleme ou trop de resine avait ete evacuee dans le drain, ce qui avait rendu ma stratification mal impregnee. Le poids des materiaux a la construction est de 3kg de tissus, et 2,1kg de resine, soit une proportion tissus resine de 59% et 41%. Le drain a pompe presque 400g de resine (soit 19% des 2,1kg, ce qui est comparable a mon test de siege). Il ne reste donc que 1,7kg de resine dans la stratification et la proportion tissus-resine est maintenant de 64% et 36%!
Malgre cela, j'ai l'impression que les tissus sont restes suffisamment impregnes. Ils ont ete bien plaques, et les bulles au niveau des surepaisseurs de kevlar (le tissus est epais et laisse des bulles quand on pose les couches suivantes) ainsi qu'a la base des pieces de styrodur ont ete eliminees.
Compte tenu de ces resultats, il me semble qu'un vide "leger" comme j'ai fait est bien suffisant, et convient a ma maniere de travailler (mise sous vide des la fin de la stratification lorsque la resine est encore assez fluide). Pour ceux qui ont une pompe plus puissante et sans reglage, il vaut mieux attendre que la resine commence a gelifier pour eviter d'en evacuer trop dans le drain (ou travailler sans drain mais la resine a tendance a s'accumuler a la surface et a faire des plis). Petite remarque: j'appelle ca vide leger, mais le styrodur a quand meme ete un peu ecrase par endroits!
Une premiere photo apres avoir enleve la bache. On voit sur le drain les taches noires qui sont causees par la resine qui a imbibe le drain (celui-ci est normalement gris). Les reliefs sont formes par la plaque de surelevation du siege et les bandes de styrodur en sandwich:
On ne voit pas le resultat en detail sur cette derniere photo, mais la coque est un peu gondolee.
C'est a cause du moule que j'ai construit leger (comme la stratification d'un bateau): la coque s'est deformee au niveau des renforts lors de la mise sous vide... voila les petits problemes qui arrivent lorsqu'on veut experimenter et ne pas faire un moule selon les regles. Je pense que ca aurait bien marche sans renfort, ou en ne mettant des reforts que sur le tour mais pas sur le fond plat.
Mercredi 9 Juillet:
Je viens de passer la premiere couche de cire sur le moule de pont. A cause de mon probleme de crapotage, il me reste pas mal d'irregularites. Je prefere les laisser et poncer eventuellement le pont du bateau lui meme apres demoulage.
Mercredi 16 Juillet: Stratification du pont.
Details de la deco: on a pose des bouts de bache plastique, fixés prealablement avec du gelcoat transparent, pour eviter qu'ils ne se deplacent lors du passage du gelcoat au pinceau.
Apres 4 heures, le gelcoat avait presque trop durci pour enlever les modeles. On a du reparer certains degats pour avoir une ligne a peu pres propre:
La stratification est un patchwok avec les chutes de la coque. Il y a 4 couches au moins sur toute la surface + beaucoup de recouvrements + une couche de kevlar sur 60cm a l'avant et a l'arriere + 2 couches de carbone sur la deco (avec des chutes en bandes), qui vont aussi participer a la rigidite du pont arriere.
Poids de tissus: 2,3kg
Poids de resine: 1,4kg
Mise sous vide: comme le pont, a savoir 500mbar immediatement apres avoir stratifie.
Poids de resine evacuee: (drain plein-drain vide): 734g-309g=425g, (soit 30% evacues). Il reste donc 1kg de resine dans la stratification
Le rapport Tissus-Resine de la stratification est de 70% de tissus et 30% de resine. Cela fait moins de resine que pour la coque (en %)! Malgre cela il me semble que les tissus sont restes bien impregnes. C'est surement plus tard que je me rendrai compte si cela pose des problemes.
La photo suivante montre le drain (normalement gris), qui s'est charge de resine (points noirs):
Ici le film de separation perfore, avec en transparent un detail de la stratification (bandes noires de carbone pour la deco et le kevlar jaune)
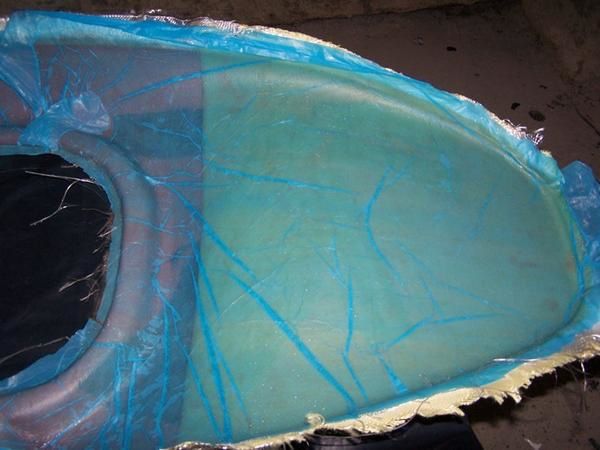
Apres demoulage, voila le resultat de la deco. Ce n'est pas parfait car la ligne orange n'est pas tres nette, mais la surface est propre, sans bulle.
Me voila pret a souder, fixer le siege etc... Je fais tout d'abord la soudure interieure avec des bandes decoupees dans du rowing (2 couches). Pour les pointes, je decoupe les bandes a 45° par rapport aux fibres; de cette maniere le tissus peut prendre n'importe quelle forme. Le siege sera colle avec au moins 3 ou 4 couches de Kevlar bi-biais.
Voila le resultat final sans les anneaux de bosse. Il pese 10kg ce qui me satisfait entierement. La ligne de soudure exterieure est en kevlar, mais j'ai colore la resine en noir parce que le kevlar perd sa belle couleur doree avec les annees. L'hiloire est de la chaussette kevlar-carbone achetee chez Zig-Zag:


Je n'ai pas un resultat parfait, et j'aimerais lister ici les points positifs et negatifs de l'operation:
Points positifs:
- le vide a tres bien fonctionne. Cela devrait repondre a la question que se posent les kayakistes, a savoir "est-il possible de construire sous vide avec une pompe de frigo?". Il faut avoir une bache bien etanche qui ne peut en general servir que pour un seul bateau, a moins de boucher les trous qui se forment inevitablement lors de chaque demoulage lorqu'on enleve le bache alors que la resine est dure et les tissus pointus...
- le sandwich rend le fond plat tres rigide ce qui devrait aider pour decoller dans la vague!
- le poids: 10kg, c'est le plus leger que j'ai construit!
Points negatifs:
- la coque est un peu gondolee a cause des renforts du moule, qui lors de la mise sous vide (et meme avant ca) ont deforme le moule. J'ai voulu faire un moule leger construit comme un bateau pour pouvoir naviguer dedans par la suite, ce qui le rend naturellement plus souple qu'un moule epais d'1cm. Dans ce cas j'aurais du faire des renforts seulement sur le tour, et pas en travers.
- l'aspect du pont n'est pas ideal car je n'ai pas repare tous les defauts produits par le crapotage du moule.
- la deco carbone est sympa, mais on voit le carbone par transparence au travers du gelcoat. J'aurais du mettre plus de colorant (bien que j'en avais deja mis 20%) ou plus d'epaisseur de gelcoat. La ligne de demarcation n'est pas reguliere: j'aurais du travailler avec du film autocollant plutot qu'avec des morceaux de bache, et les decoller un peu plus tot. Peut etre j'aurais aussi du charger la resine avec un peu plus de silice pour eviter qu'elle coule.
- la ligne noire de soudure exterieure n'est pas propre car j'ai utilise du scotch de peintre en papier au lieu d'utiliser du scotch marron en plastique. Ce dernier a tendance a laisser de sales traces, mais dans mon cas (bateau sorti du moule) je n'ai pas eu ce probleme.
Tout cela pourra etre ameliore lors d'un prochain bateau. Cependant, faire un moule tout seul demande beaucoup d'energie, et je m'orienterai dans le futur probablement de nouveau vers la methode "one-shot". C'est la methode la plus rapide pour pouvoir naviguer rapidement dans son bateau.
Thanks to Mihai ( http://freeridemihai.multiply.com/photos/album/32 ) for these last pictures:
8 mai 2008
4
08
/05
/mai
/2008
23:22
TEST SOUS VIDE GRANDEUR NATURE Premier test de ma pompe avec la bache que j'utiliserai pour construire mon bateau sous vide. C'est une bachede 80µ d'epaisseur (noire malheureusement). Je l'ai scotchee avec le classique "scotch marron" en faisant 2 ourlets pour ameliorer l'etancheite. Pour l'instant il n'y a pas de probleme: avec le vide regle a 350mBar residuels, le rapport temps de marche/ temps d'arret est de 13sec/ 40sec. Il faudra quand meme faire attention aux trous quand je mettrai le moule dedans... vu le debit de ma pompe je pense qu'un trou meme petit pourrait compromettre la mise sous vide. Pour l'aspiration, j'ai achete un tube d'arrosage renforce. Il est perce tous les 10cm sur les 2 premiers metres qui sont enfermes dans la bache. Ca permet d'avoir une aspiration reguliere sur toute la longueur du bateau. Ici la photo d'un gros duvet bien comprime. Si vous ne voyez pas grand chose, c'est normal il est vraiment aplati:
Detail de la fermeture avec un serflex. Apres avoir chronometre le rapport marche/arret de la pompe, j'ai rajoute qq tours de tournevis, ce qui a encore ameliore l'etancheite.
TEST DE KEVLAR
J'ai la possibilite d'avoir du kevlar vraiment pas cher. Je m'en suis fait envoyer un echantillon pour voir si ca me convenait. Il est assez raide et je voulais donc le tester avant d'en acheter de grosses quantites (quoi qu'a ce prix il faut pas trop reflechir je pense).
J'ai donc fait une forme en polystyrene avec un gradient de courves, allant de la courve legere jusqu'a l'angle droit la ou la piece rejoint la table (photo). Ce n'est pas le tissus le plus facile a former mais il se laisse quand meme travailler... ca me rappelle un peu le diolen. Il ne prend pas les angles les plus difficiles, mais je pense que ca ira tres bien pour la construction sous vide, et surtout pour une coque ou il n'y a pas trop d'angles. Une fois stratifie avec un tissus plus souple, en l'occurence du rowing 280, il prend mieux les courves (strat.: KVKVVK).
15-06-2008: CONSTUCTION D'UN SIEGE SOUS VIDE. Avant de me lancer dans la construction d'un bateau je dois tester le travail sous vide, la resine, la couleur etc... faire un siege est la bonne occasion pour ca. Faire une siege sous vide n'est pas vraiment necessaire, mais c'est juste pour tester la methode de travail. Gelcoat: on m'a vendu de la silice a melanger a mon epoxy pour en faire du gelcoat. J'ai attendu 12h avant de stratifier. Resine Epoxy: On m'a dit que le dosage en volume est le meme qu'en poids (1 Part Resine + 1/2 Part Durcisseur). La prise n'est pas tres bonne, et apres 3 jours je peux encore faire une petite marque avec l'ongle. Vide: J'ai mis sous vide assez leger (500mBar) pendant la premiere 1/2heure, puis j'ai diminue jusqu'a 350mBar residuels. Le vide s'est tres bien fait jusqu'a la 4e heure ou j'ai voulu ouvrir pour voir (impatience, impatience...). Cette experience m'aura montre qu'avec l'epoxy il faut etre patient, puisque la resine n'etait pas prise. J'estime la quantite de resine qui a ete drainee a 120-150g ce qui est beaucoup puisque j'ai mis a peine plus de 300g dans ma strat (45 a 50% evacues). Il faut donc que je revoie ma procedure de mise sous vide. Detail du siege une fois demoule, avec un essai de deco. C'est pas encore ca, mais je voudrais mettre des chutes de carbone qu'il me reste, et passer du gelcoat transparent a ces endroits. C'est difficile de dessiner proprement il faut que je trouve une solution avec des calques que je peux enlever par la suite:
Detail du plastique perfore et du drain qui boit l'exces de resine. Plastique perfore a ete achete chez ZIGZAG, et le drain est un genre de moquette ou de feutre fin (2 ou 3 mm) achete dans un magasin de bricolage.
CONSTRUCTION D'UN 2e SIEGE: Vus les resultats pas tres convaincants du premier siege, je fais une 2e piece pour ameliorer le dosage de la resine et la procedure de mise sous vide. En ce qui concerne le vide, je voulais proceder un peu plus methodiquement, p.ex: 4h a 600mBar residuels, puis descendre a 350. Je suis finalement reste a 550mBar residuels pendant 8-9h parce que j'ai du partir et ne pouvais pas surveiller. J'ai aussi laisse une part de la surface sans drain pour voir la difference lorsque la resine n'est pas evacuee. Apres demoulage, je me rends compte que ce n'est pas optimal car il y a une accumulation de resine a la surface et ca laisse des plis de resine. Pour la precision du dosage resine, j'ai achete une balance de cuisine digitale, precise au gramme. Ca me permet aussi de connaitre le poids des tissus, et la quantite de resine evacuee: - Poids de fibre 400g - Poids de resine: 340g - Quantite de resine evacuee (le drain a ete pose sur seulement env. 65% de la surface)= 47g Ce sont donc 70g de resine qui auraient ete pompes si le drain avait ete pose sur toute la surface, soit 20%. Le siege est cette fois costaud, et il me semble qu'un vide leger comme je viens de faire m'assure une certane securite quand a la quantite de resine evacuee, et au moins une certaine compression des couches au debut de la polymerisation. Trop de resine a ete evacuee lors du premier siege, parce que j'avais mis trop de depression des le debut, et il vaut mieux etre prudent a ce niveau la!
15 avril 2008
2
15
/04
/avril
/2008
18:40
Il s'agit cette annee de modifier legerement le pont de ma forme de l'an dernier, puis de faire un moule.
Le but final de l'operation est de faire un kayak sous vide en epoxy. C'est un vieux reve que je veux enfin realiser, meme si je n'aurai surement pas un resultat professionnel.
Samedi 26 Avril 2008:
J'ai fini de preparer la coque. Elle est maintenant:
- poncee: d'abord au gros papier (grain 80 voire 40) pour enlever les grosse irregularites. J'ai ensuite passe une couche de glacage que j'ai poncee au papier de verre a l'eau, avec des grains successifs 120, 360 et 600,
- polie: avec un polish qui donne un effet brillant mais n'efface pas les traces du grain 600.
- ciree. J'ai utilise comme l'an dernier de la cire liquide: 3 couches de cire sans lustrer pour eviter que le demoulant ne perle, puis 1 couche de demoulant liquide.
Je suis donc pret a faire le moule. Je vais stratifier de maniere a pouvoir utiliser le moule comme bateau une fois que je ne voudrai (ou ne pourrai) plus construire de bateaux dedans. Ca permettra d'eviter de l'envoyer a la poubelle directement. Je vais donc mettre 5 couches de rowing 280g avec un mat 30g en premiere couche. A la place du gelcoat interieur, je vais mettre une couche de resine normale pour gagner un peu de poids.
Lundi 28 Avril: Demoulage!
Ca s'est passe sans probleme. La surface est pas trop mal, et c'est reste bien brillant. Par contre en y regardant de plus pres on voit le quadrillage du rowing malgre le mat 30g que j'avais mis en premiere couche.
Mercredi 7 Mai: Renforts du moule, avec 1 ou 2 couches de mat epais. C'est maintenant bien rigide. MISE A JOUR: lors le la construction du bateau je me suis rendu compte que ces renforts ont pose des problemes avec la stratification legere que j'ai faite: lors de la mise sous vide, le moule s'est deforme localement au niveau des renforts. Donc a eviter si vous faites un moule leger comme moi et que vous voulez construire sous vide.
Au dessus, on voit le moule de siege que j'ai ponce et glasse.
Jeudi 8 Mai: premier essai de vide grandeur nature! Je suis donc pret a construire sous vide. J'hesite maintenant entre faire le moule du pont, ou construire d'abord une coque en epoxy... j'aurai un petit probleme de stockage si je construis la coque et que je traine ensuite pour faire le pont.
Dimanche 18 Mai: moulage du pont.
J'avais commence a faire des motifications de volume avec du platre, mais vu l'etendue des travaux, j'ai tout enleve et je laisse la forme comme elle etait.
La seule modification que je fais est la decoupe de gouttieres de chaque cote de l'hiloire pour evacuer l'eau. J'ai decoupe les encoches a la Dremel, puis reformé avec du platre. J'ai ensuite fait un glacage avec 2 couches de resine comme le reste du bateau:
Detail de la stratification (de l'interieur vers l'exterieur):
- 1 mat 30g comme pour la coque, pour que la "resine-gelcoat" accroche (je ne mets pas de gelcoat mais simplement une couche de resine avant de stratifier)
- 1 silione 160g (tissus avec tissage fin) pour essayer d'eviter l'effet relief qu'a donne le rowing sur la coque
- 3 rowing 280g
- 1 mat 30g a l'exterieur pour le poncage quand je souderai le moule pour l'utiliser comme bateau.
Je ne resiste pas a l'envie de mettre une photo avant demoulage, j'adore la couleur!

Samedi 24 Mai: Demoulage du pont. Ca a ete facile, par contre j'ai une collection complete de problemes de surface: crapotage et bulles! Il y a du boulot pour rattraper ca. Je viens de poncer les endroits abimes, et passe une premiere couche de resine. Je vais passer une seconde couche, voire une 3e, puis poncer pour rattraper la surface. J'etais tellement énervé que je n'ai pas pris de photo, j'avais juste envie de réparer ca le plus vite possible.
Le point positif est que le silione 160 en seconde couche a bien evite l'effet relief du rowing,
Samedi 31 Mai: J'ai passe 2 autres couches de resine sur les endroits abimes, et commence a poncer. Ca prend du temps, mais je devrais arriver a un resultat satisfaisant.
La suite...: la construction du bateau!
1 avril 2008
2
01
/04
/avril
/2008
21:55
Voila la presentation de ma pompe a vide a partir de 2 compresseurs de frigo branches en parallele. L'idee de faire des kayaks sous vide en utilisant des pompes de frigo est assez controversee, mais je commence a me faire une idee sur la question.
L'argument le plus souvent rencontre est qu'une pompe de frigo n'est pas assez puissante, que c'est juste bon pour les modeles reduits et pour les surfeurs qui stratifient sur de la mousse et ne doivent donc pas trop descendre en depression. Il y a deux parametres a prendre en compte pour repondre a cette question: le vide et le debit que la pompe est capable de produire.
Vide: pour avoir teste plusieurs pompes de frigo avec un vacuometre, on arrive sans probleme a 0,1 bar de pression residuelle (0,9 bar de depression) pourvu qu'il n'y ait pas de fuite. Une fois reglee a 0,35 bar (soit 0,65 de depression), le systeme entier de pompe que j'ai monte a un rapport temps de marche / temps d'arret de 7sec/50sec.
Quand au debit, il est faible. C'est vraiment le parametre limitant, et c'est la raison pour laquelle j'ai deux pompes sur mon systeme. Le sac dans lequel la piece est mise sous vide doit etre tres etanche et c'est le point clef pour un bon fonctionement. Je n'ai pas encore construit de coque sous vide, mais je pourrai en dire plus dans quelques semaines. MISE A JOUR: apres fabrication du kayak, l'experience montre qu'une bache bien etanche permet de construire un kayak sous vide sans probleme, meme avec un seule compresseur de frigo!
En ce qui concerne la construction du systeme, il y a deja plein d'infos sur le net. Le systeme de regulation a ete monte par mon grand-pere modeliste de longue date. J'ai eu le droit de me servir chez lui puisqu'il en avait deja plusieurs.
Voila le systeme complet avec:
- la bouteille tampon: elle n'est pas indispensable mais permet de reduire la frequence d'allumage du moteur. Penser a la remplir d'eau avant utilisation, pour vider les eventuells restes de gaz inflammables.
- le systeme de regulation: il permet de stopper le moteur lorsque la depression a atteint un niveau defini. Ce n'est pas indispensable, mais interessant neanmoins pour connaitre a peu pres la depression. Cela permet de regler la depression en fonction de la fluidite de la resine epoxy. Je ne peux pas donner plus de details sur le branchement electrique, mais le principe de la regulation avec le declencheur a membrane est assez bien explique sur le site de Mardo.
- la distribution des tuyaux d'air. J'ai 5 entrees: 1 pour l'admission d'air, les 2 derivation pour la bouteille tampon et le declencheur de clim, puis 2 sorties vers les compresseurs.
- je n'ai pas de derivation supplementaire pour un vacuometre mais j'en ai utilise un pour etalonner le systeme de regulation
- la bouteille plastique au tuyau de sortie du moteur pour recuperer l'huile qui est evacuee par les compresseurs.

Lors du branchement du moteur il vaut mieux ouvrir la "boite noire" et demonter les deux cables dont les fils sont branches sur les differentes broches. Le mieux est de tout enlever et de rebrancher correctement un seul cable. Pour cela, prenez un cable a 3 fils et connectez le fil bleu a la bobine (ou bien a une des broches qui y sont reliees). Ensuite il faut trouver la broche ou brancher le fil marron: c'est en general une broche situee au dessous de la bobine, du moins c'est le cas sur mes deux moteurs. La masse (jaune et vert) sera branchee la ou la masse allait dans le branchement original.
La photo suivante montre le branchement original du cable d'alimentation. Comme ca ne fonctionnait pas dans cette position, j'ai juste debranche le fil marron et l'ai rebranche sur la broche "C".
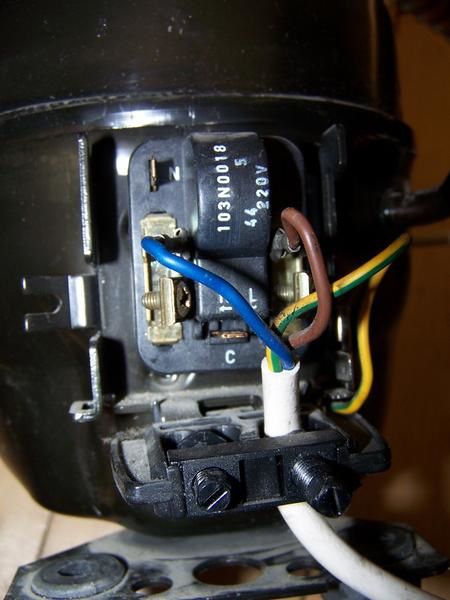